The electronics industry is fast approaching the lead-free deadline first established by the European Union. Almost all electronic components are connected with solder, which traditionally contains lead because of its low melting point and relatively high strength. Finding a lead-free soldering process is a problem many manufacturers face. Not only does a sufficient lead-free solder need to be identified and tested, but also the equipment for a lead-free process needs to be purchased. With over 150 patents globally, the selection of the right solder can be daunting. Some companies will not meet this deadline because the transition is more complex and time-consuming than anticipated. This article explores some of the considerations that companies must make when switching to lead-free solder and equipment
Ag: silver |
Cu: copper |
Pt: platinum |
Al: aluminum |
In: indium |
Sb: antimony |
Au: gold |
Mo: molybdenum |
Sn: tin |
Bi: bismuth |
Ni: nickel |
W: tungsten |
Cd: cadmium |
Pb: lead |
Zn: zinc |
Cr: chromium |
Pd: palladium |
Abbreviations appearing in this article
Kester, one of the leading global suppliers of high performance interconnecting materials says that the two main alloys are variants of Tin-Silver-Copper and Tin-Copper.
"These alloys have higher melting temperatures and wet metal surfaces more slowly, the joints also look different in that the surfaces are not as reflective as tin-lead joints. The flux chemistries that worked well with a leaded process are not the best fit for lead-free soldering."
Changes have been made to solder pastes for both no-clean and water soluble assembly and wave solder fluxes (alcohol and VOC free) to achieve better compatibility to lead-free solder. Solder bars, solder preforms, tacky solder fluxes, solder spheres, and bumping pastes have all been re-designed to improve performance. Although these alloys don't have the same properties as lead based solder, they have been thoroughly tested and are and adequate replacement for most applications.
One alternative is Fujitsu's introduction in June 2002, of tin-zinc-aluminum solder. Besides having a lower melting temperature (199°), it is also less expensive because tin, zinc, and aluminum are all widely available materials and it doesn't contain silver. It doesn't change existing soldering processes and is within the heat tolerances of most components. According to Fujitsu magazine, "Fujitsu has already used PC boards containing the new lead-free solder in some products, and plans to extend its use to other products." Fujitsu noted on their website though that distribution is limited to certain fields because joint reliability problems caused by a reaction to lead contained in existing terminals
Here is a list of key variables to consider when using lead-free solder for surface mounting (SMT) and through-hole components:
Alloy melting temperature
Flux chemistry - activation, temperature effects
Wetting and surface tension properties of the alloy
Solder balling and bridging potential increases
Component/board reliability
Compatible rework/repair processes
Compatible wave, selective soldering process
Quality inspection criteria
Cosmetic effects of flux at higher reflow temperatures
Nitrogen vs. air
Pin testability of flux residues
Solder voids impact
Residue cleaning/removal process changes
Compatible conformal coating and under fill materials
Oven maintenance and flux decomposition volumes (Biocca)
Temperature Considerations
Alloys | Melting Range |
Sn63/Pb37 | 183°C |
Sn99.3/Cu0.7 | 227°C |
Sn96.5/Ag3.5 | 221°C |
Sn95.5/Ag4/Cu0.5 | 217 - 218°C |
Sn96/Ag2.5/Bi1/Cu0.5 | 214 - 218°C |
Sn96.2/Ag2.5/Sb0.5/Cu0.8 | 210 - 216°C |
Lead-free solder alloys usually have higher melting temperatures than tin-lead or tin-lead silver for example, which have a melting point of 183°C. As shown in the above table, tin-silver-copper (SAC) solders have melting points in excess of 217°C. Reflow process and the wave solder pot temperatures are higher and boards and components are subjected to this higher heat for longer durations. The board itself could sag during pre-heating or wave contact, so design engineers have recommended a center support for boards to increase stability and solder yield. Thermal fatigue of the solder joint influences the reliability of electronic assemblies too. The size of particles in fumes is smaller and more abundant; so not only does the high temperature make the cost of production higher, but also increases the risks from emissions.
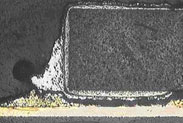
Thermal fatigue causes solder to rupture |
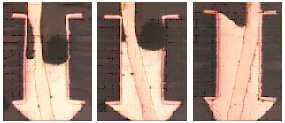
The degree of hole-fill increases as temperatures increase for 240, 250, to 260. |
Defects
"The main concern with lead-free soldering is the potential increase in soldering defects," says Biocca of EMSnow. These defects increase with a poorly optimized lead-free wave process:
Tearing
Insufficient solder
De-wetting
Icicling
Cold solder joints
Grainy joints
Blow holes
Solder balls
Fillet lifting
|
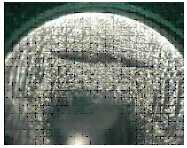
Tin-rich solders cool rapidly causing a heat tearing effect. |
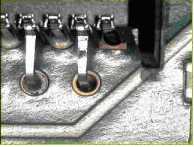
Insufficient hole-fill. |
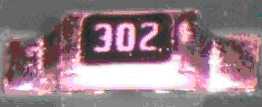
Well soldered SMD bottom-side
|
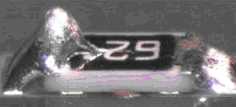
Icicling of SMD using No-Clean POLO flux |
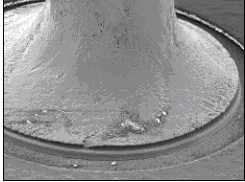
Fitting lifting, photo by Bob Willis
|
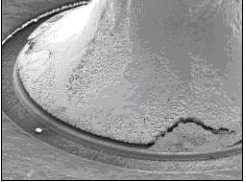
Fitting lifting with cracking, photo by Bob Willis |
According to Biocca, new liquid fluxes have been developed that contain higher levels of solids with activators and more aggressive ingredients, which have been proven to give the best hole-fill with lead-free, even on more difficult surfaces like bare copper. They reduce surface tension by limiting the amount of oxides on the surface. Although they may be corrosive, excess activators in the fluxes can remove all the oxides adequately even with the longer contact times and hotter soldering temperatures.
Manufacturers have environmental concerns about these newer fluxes containing volatile organic compounds (VOC). Organic compounds like alcohol are commonly used in these fluxes. Alphametals conducted a study to determine the wetting properties of VOC-free compounds where instead they used water as a solvent base. They measured wetting time, angle, balance, and wetting force. Information on this can be found at http://www.alphametals.com. Basically they concluded that although these compounds did not perform as well, they did perform satisfactorily where lead-free is perceived as necessary.
In most cases, soldering results were satisfactory in air, but some problem assemblies produced bridges or icicles. These results were improved with a nitrogen atmosphere.
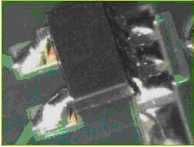
Exposed copper on bottom-side SMD
|
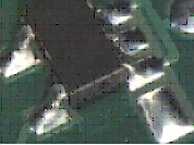
Nitrogen used at solder pot |
Just like with lead-based solder, there are many choices that are commonly used. The general trend is leading toward variations of tin-silver-copper alloy and the fluxes, solvents, and pastes that have been developed for their application. When searching for a lead-free solder, keep in mind the cost, temperature, environment, and process compatibility issues. Many classes, seminars, and training sessions are available on the subject to help with the transition. The final product is really what determines the best choice and most manufacturers can help consumers with their decision.