There are literally tens of thousands of relay varieties on the market. Knowing which relay to choose for your application can be critical to its success because each type of relay has its advantages and disadvantages. Designers must consider cost, reliability, durability, rating, voltage, function, size, and number of contacts just to name a few things. In many cases any number of relays can do the job and other times it takes a certain relay. This month's article focuses on the most common relay types: electromechanical, reed, and solid state.
Electromechanical relays
As the name implies, electromechanical relays (EMR) use electricity to move mechanical parts in order to open and close the contacts. In the figure below, an armature is moved by a magnetic field produced by a coil in order to bridge the contacts. EMR's are generally larger and more durable with larger contacts that make them more resistant to electrical surges. The tradeoff comes when the large size and magnetic current make it difficult to place compactly in a module. Plus, compared to other types of relays, they are relatively slow with a 5 - 15 ms switch time. Recent innovations, though, have significantly reduced the size and improved performance characteristics especially for the telecommunication field.
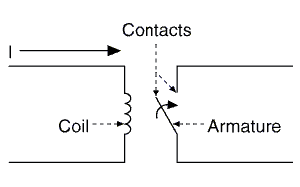
In general, there are two types of EMR's: latching and non-latching. Latching relays remain in the position they were last switched to even when current stops. They are well suited for applications that want to limit power consumption. Non-latching relays, whether normally open (NO) or normally closed (NC), return to their default positions once current stops flowing.
EMR's are good all purpose relays that have a few limitations. If switching speed and size are not major concerns and versatility and variety are, these are the relays of choice.
Reed Relays
Reed relays could be considered a type of EMR because they have parts that move as a result of electrical current, but their look, function, and performance vary considerably. [See Fig. 2] They have much smaller, less massive contacts and a different actuating mechanism, which allows them to switch about 10 times faster than an EMR with equivalent ratings.
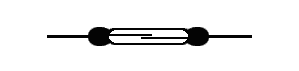
Hasco's products have been tested in hundreds of millions of cycles. Just as important than having a reed go on and off is the long life at low current, even after many years of inactivity. This is critical in life safety applications. They are so reliable because the reed contacts are hermetically sealed in glass with an inert gas. This keeps contact resistance to a minimum and shields them from the environment.
Reed switches are commonly used with magnets to open or close a circuit in applications requiring low and stable contact resistance, long life, and small size. An example of their use would be the alarm sensor, known as a magnetic contact, on doors or windows. Another popular application for their use is in liquid level sensors where the reed switch is stationary on a wall and the magnet is on a float that moves up and down.
Solid State Relays
Solid State Relays (SSR) have no moving parts. They have many advantages over EMR's such as no acoustical noise, low controlling power, no contact bounce or arching, minimal space requirements and a long life expectancy. The high-powered models are generally much less expensive than the equivalent EMR, but the low power AC ones in most cases are more costly. This is tied to the fact that the contact resistance for an SSR is greater because the connection is made via a transistor instead of physical metal like in electromechanical and reed relays.
Many electronic designs can take advantage of the improved performance and small size of SSR's. They are commonly designed to use a photosensitive Metal-Oxide-Semiconductor Field-Effect-Transistor (MOSFET) device with a Light-Emitting Diode (LED) to actuate the device. [Fig. 3]. This type of SSR is commonly housed in Dual-Inline-Packages (DIP's) and use Single-Pole, Single Throw (SPST).
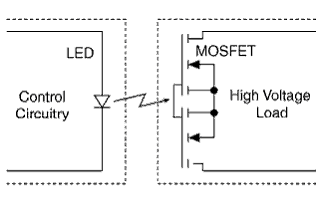
The buffer between the LED and the MOSFET makes these relays well suited for high voltage applications although, much like reed relays, they are highly susceptible to surge currents and damage when used at signal levels above their rating. Even without contacts that can weld together like with other relays, damage to the MOSFET can render the relay unusable.
Summary:
The table below provides a brief look at some of the pros and cons for each type of relay.
Electromechanical | Reed | Solid State |
Pros:
low cost
large variety
durable
usually fail in open mode (safer) |
Pros:
reliable
small and light
low power consumption
leakage current much lower |
Pros:
very long life cycle
no contact bounce
high performance
no noise
|
Cons:
slower switch time
limited contact lifetime
take up large space |
Cons:
sensitive to magnetic fields
sensitive to large surges
sensitive to vibration |
Cons:
usually fail in the closed mode
more expensive
|
As the RoHS directive deadline has passed, most relay companies have switched to lead free versions for all their relays. Contact your relay supplier with any questions or concerns regarding compliance or performance issues.
|